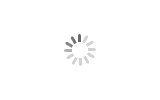
Industrial Extruded Radiator Aluminum Profile Mold
Brand Customizable
Product origin Shandong, China
Delivery time 15-45days
Supply capacity Annual output 6,000 tons
Industrial aluminum profiles have consistency, making them cost-effective.
Aluminum extruded radiator have a wide range of uses.
What is aluminum extrusion mold
What is aluminum extrusion mold
Extrusion is a manufacturing process that produces aluminum alloy solid, hollow, semi-hollow and customized profiles. It involves pushing a heated aluminum billet or bar (400-480°C) using a punch, forcing the material to flow inside a aluminum extrusion mould and permanently deforming it into the desired component according to the aluminum extrusion mould. Therefore, the design and construction of the aluminum extrusion mold is critical to the process.
Most industrial aluminum extruded radiator have strict requirements on materials, performance, dimensional tolerance, etc. Although the profit of industrial aluminum extrusions is higher than that of Building aluminum profiles, its production difficulty is relatively large and the technical requirements are also high.
Key factors affecting aluminum extrusion mold:
Key factors affecting aluminum extrusion mold: The die hole shape and diversion hole layout of the die design. The uniformity of metal flow can be adjusted by modifying the die by filing the obstruction corners, welding or pitting.Parameters such as extrusion speed, temperature and pressure must be accurately matched. Uneven metal flow rate will cause ripples or deformation; insufficient temperature will cause a sudden increase in extrusion pressure and damage the die.
Advantages of Industrial aluminum extrusions
Industrial aluminum extrusions have strong design flexibility due to their unique processing technology and material properties. They can produce hollow, multi-cavity or multi-porous sections to meet special functional requirements. They can also be customized and are suitable for small batch customization.
Extrusion can create complex shapes and contours that may not be possible with other manufacturing methods, allowing designers to create custom components for specific applications. For example, certain features, such as sharp corners, are difficult to manufacture via CNC, and sometimes custom industrial aluminum extrusion shapes can solve the problem.
Aluminum extruded radiator vs. die casting and CNC machining parts
Features | Aluminum extrusion parts | Die casting parts | CNC machining parts |
Complexity | High, 2D cross section | High, 3D cross section | Very high, free-form surface |
Cost | Medium-low, large batch | Low, large batch | High, small batch |
Strength | Medium-high | Medium, porous | High |
Production speed | Fast | Very fast | Slow |
The advantages of aluminum extruded radiator are design freedom, light weight and low overall cost. They can produce structural parts with special requirements for cross-sectional shapes and are widely used in the industrial field.